Maximize manufacturing execution with HPC
Traditional manufacturing execution systems (MES) are no longer capable of delivering efficient production turnaround and track-and-trace requirements. To overcome these limitations, MES should be enhanced by integrating high-performance computing (HPC).
Particularly as the industry shifts towards ‘more than Moore’ sysems based on multi-chip modules and various chiplets, MES has inevitably become more complex. Trying to manage each single device within an end product involves steps that sequentially add seconds rather than milliseconds to fabrication, assembly and test. This adds delay and increases the risk of error or insufficient traceability.
The trace factor is especially important given end-customer demands for better zero-defect products and the requirements of SEMI’s T23 standard for single-device traceability. Research has revealed that 72 per cent of customers demand higher quality and they are exerting pressure to shorten new product introduction times.
A white paper from Siemens EDA discusses this challenge and describes how HPC within MES charts the way forward.
It considers the complexity of the track-and-trace process, one that is often seen as interchangeable but which in reality defines two discrete though sometimes similar objectives (Figure 1). It also highlights how fab throughput is now rising to match yield as a key metric for fab performance.
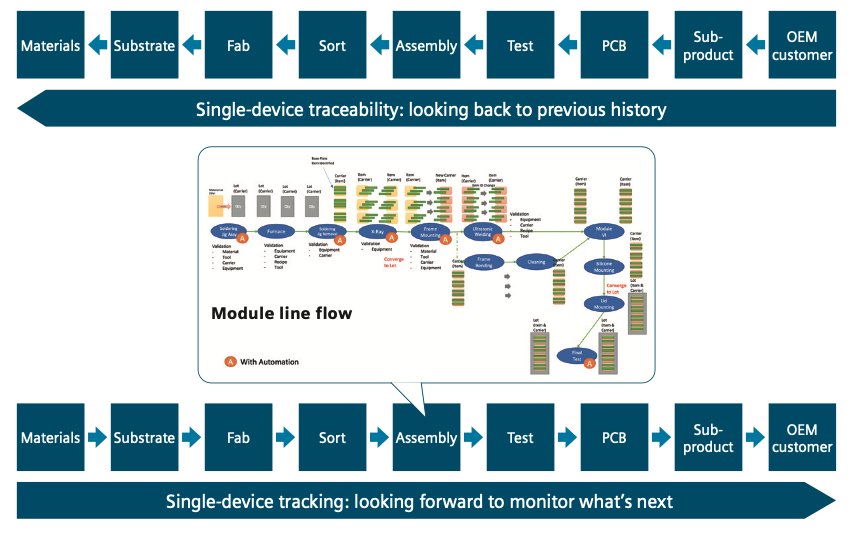
Figure 1. Single-device traceability requires single-device tracking, which can be complex at every step (Siemens EDA)
Within this context, the data points that must be addressed for each component – or single device – within an MCM or multi-chiplet end-product can quickly run into the thousands.
HPC can help enhance an MES because it enables a move away from more time-consuming sequential analysis and data writing, as the authors explain.
“Anytime a parent lot needs to break into 50 or more child transactions, a high-performance engine (HPE) will be more effective. HPE uses bulk, not sequential, data writing. This enables thousands of transactions in the data- base using stored procedures,” they write.
“To avoid unduly slowing down the application, HPE performs these bulk writes to the database, not on the application server. Keeping writes at the database minimizes network chatter and keeps speed high. It can write database actions, parameters, statements or values.”
They also list the qualities of that an MES system integrated with HPE now requires:
- HPE: For rapid processing of many transactions simultaneously configured for semiconductor tracking needs.
- Two-level dispatching: Two-level lot starts for parent and child lots that recognize the relationship between work order and quantity of lots.
- Multi-dimensional carrier positions: Ability to configure 2D or 3D tracking with position availability.
- Child load/unload: User interface and transactions for child container load into new positions in the carrier.
- Item tracking modes: Three modes of item tracking – lot, carrier, or individual item wafers.
- Verifications: Able to configure carrier-loading verification.
- Automated and manual access: Supports complex flows and item tracking by carrier, whether materials movement is automated or manual.
- Multi-container closure: To close or terminate multiple lots, items or carriers, ensuring child lots carry forward the correct attributes.
Finally, the papers outlines how these goals for the MES can be met using the Opcenter Execution Semiconductor suite for fabrication, assembly and test.
‘Single-device tracking for semiconductors’ is available to download here.